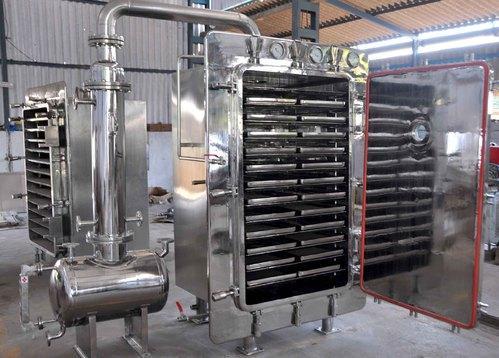
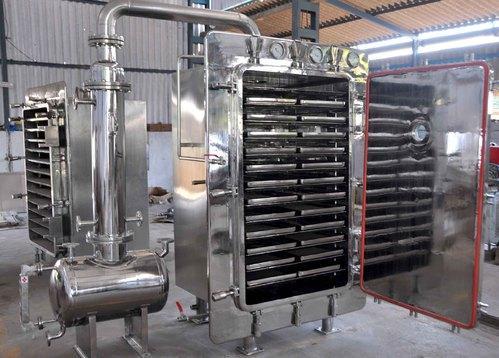
Vacuum Tray Dryer are used where heating and drying are essential parts of manufacturing process in industries such as Chemicals, Dye stuff, Pharmaceutical, Food Products, Colors etc. Vacuum Tray Dryer is suitable for drying of thermal sensitive material easily deteriorated under higher Temperature. It eliminates configuration damage of the drying materials.
SALIENT FEATURES :-
Bodies may be of cylindrical or rectangular cross section. Both shelves and body are heated (the body to prevent internal condensation) with controlled circulation of hot water, steam or dia thermic fluid. Vacuum is drawn through large diameter ducts to minimize pressure drops and produce minimum working pressures. Both rotary and static dryers can be supplied with the following Optional ancillaries.
- Heater system for either pressurized hot water or dia thermic fluid.
- Cyclones and sleeve filters for powder recovery (for rotary dryers)
- Solvent recovery system with condenser and receiver, vacuum pump and ancillaries, characteristics and dimensions depending on the drying processes.
Vacuum tray dryer working principle
Specifications:
Model | VTD6 | VTD12 | VTD18 | VTD24 | VTD36 | VTD48 | VTD96 |
---|---|---|---|---|---|---|---|
Number of Trays | 6 Trays | 12 Trays | 18 Trays | 24 Trays | 36 Trays | 48 Trays | 96 Trays |
No. of shelves | 6 | 6 | 6 | 8 | 12 | 16 | 32 |
Dummy Shelves | 1 | 1 | 1 | 1 | 1 | 1 | 2 |
Trays per shelves | 1 | 2 | 3 | 3 | 3 | 3 | 3 |
Housing Construction | Mild Steel / Stainless Steel 304 / 316 / 316L | ||||||
Doors | Mild Steel / Stainless Steel w/ inter lock & glass wool insulation | ||||||
Hinges | Stainless Steel | ||||||
Heating Material | Water / Fluid | ||||||
Heating Shelves | SS /Hollow Pad Type, baffled for essential heat transfer | ||||||
Trays | Food Grade Stainless Steel | ||||||
Tray Size | 16 x 32 x 1.25 (inch) | ||||||
Insulation | Thick glass wool | ||||||
Controls | PID Controller | ||||||
Vacuum gauge | Dial type located on vacuum chamber | ||||||
Temperature Indicator | Digital | ||||||
Pressure release valve | Yes | ||||||
Vacuum break valve | Yes | ||||||
Limit Switch | Yes | ||||||
Optional | – Circulation pump with FLP Motors and controls – Vacuum Pump (2stage water ring) consisting FLP motor – PLC controller – Nitrogen purging valve – Validation ports w/ sensors – Condenser-Shell & tube type – Condensate Receiver – Viewing glass – Shell & tube type condenser – IQ / OQ / DQ / PQ Certifications |
||||||
Certifications | CE, ISO, cGMP |
We involve in designing and producing vacuum tray dryers that are used in laboratory, pharmaceutical, food, and cosmetic industries. With a team of professionally talented engineers we provide custom design facilities to its customers and they are welcome to discuss their requirements including vacuum tray dryer design, size, number of trays, required temperature, optional accessories etc. We are promising full customer satisfaction and unmatched quality service. All these units are supplied with full installation, commissioning and training at customers’ workplace. We also export our vacuum tray dryer equipment to all over Asian, African and Middle East countries at factory price.