Double Helical Ribbon Blender
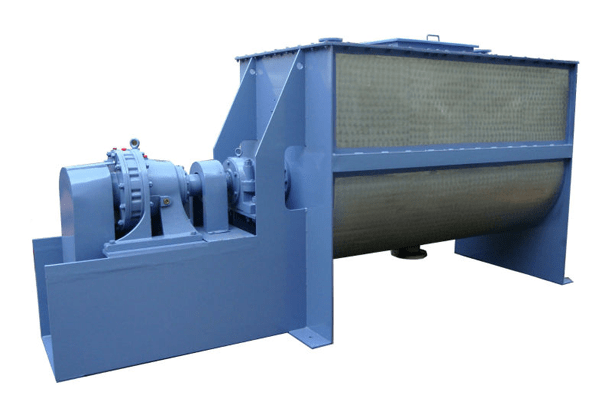
Description
Double helix ribbon mixer machine for powder and liquid mixing is widely used in mixing dry powder, granule, particle, liquid and paste materials with low viscosity. Horizontal double helix mixer with high speed crushing choppers is based on horizontal ribbon blender by setting several units of high speed chopper blades on side of the U shaped Blending barrel.
We also can Manufacture Customized Double Helical Ribbon Blender consists of a horizontal U-shaped trough containing a rotating double helical ribbon agitator inside. The horizontal agitator shaft is located in the center of the trough on which the helical ribbons are provided. A sealing arrangement is provided for the area where the shaft exits the container to ensure that material does not travel from the container to the outside and vice versa. The blender assembly along with the drive system components such as the motor, gearbox, couplings and bearing supports are mounted on a supporting frame.
Consisting of a combination of inner and outer helical ribbons, the ribbon agitator is referred to as the “double” helical ribbon agitator. The external ribbon flights move the material from the ends to the center during the blending operation, while the inner ribbon flights move the material from the center to the ends. Because of the rotational motion of the ribbons, radial mixing is accomplished. Axial movement of the material along the horizontal axis of the blender stems from the disparity in peripheral velocities of the outer and inner ribbons. As a consequence of the radial and counter-current axial motion, homogeneous blending with 90 to 95 percent or better homogeneity is achieved within 15 to 20 minutes of start-up. The biggest effect on the mixing efficiency of the ribbon blender is the solid particle size and its bulk density. As compared to ingredients with variance in these properties, ingredients with similar particle size and bulk densities tend to blend faster.
The material loading in the blender normally takes place by means of nozzles or feed-hoppers located on the blender ‘s top cover. The ribbon blender ‘s working capacity ranges from 40 to 70 percent of its total volumetric capacity. The product is discharged from a discharge valve located at the bottom of the trough after blending. Depending on the size of the blender, more than one discharge valve may be provided. The valve operation may be manual or pneumatically actuated. In the ribbon blender, obtaining 100 percent discharge is practically difficult. The amount of hold up after discharge in the blender depends on the material properties, the clearance between the ribbon flight’s outer edge and the blender container’s inside wall. Depending on the application, a clearance of 3 mm to 6 mm is usually maintained.
Helical Ribbon Blender Working Principle
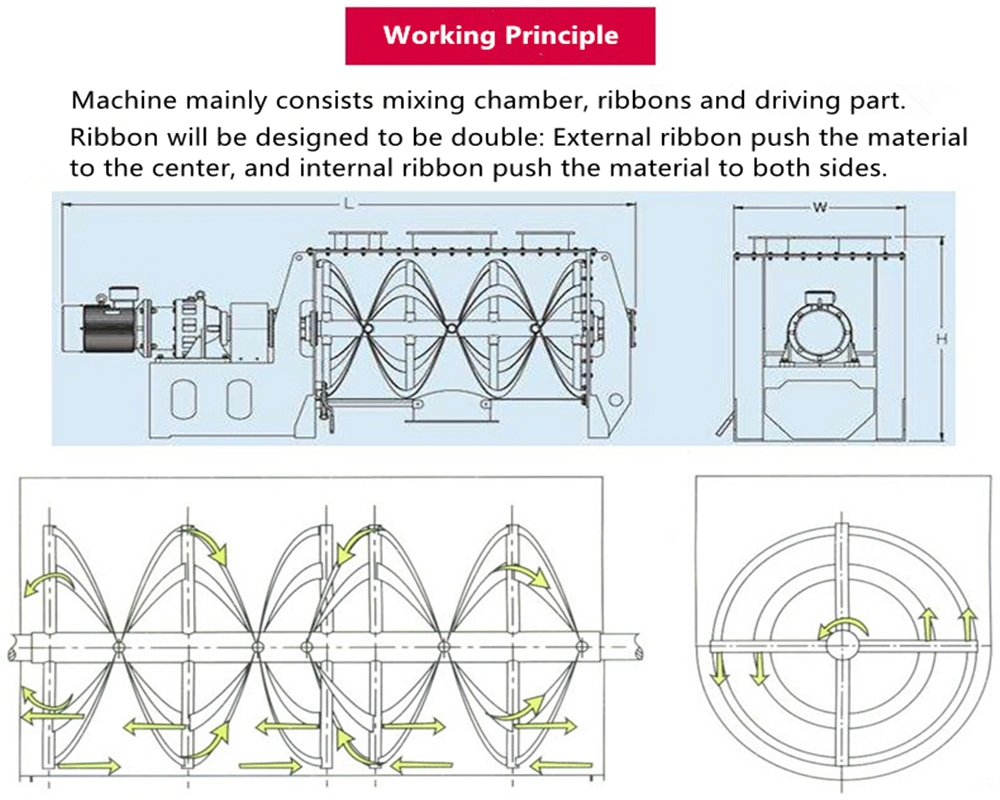
Principle and features:
The vortex outer ribbon combined with rotating direction drives material from two sides to the center, meanwhile inner ribbon drives material from center to two sides, and the high speed chopper blades could break and disperse the lumps and blocking.
Therefore horizontal double ribbon mixer with crushing chopper blades can especially meet the demands of various kinds of blending powdery materials which may easily gather together during the mixing process. Horizontal ribbon blender machine with high speed choppers is your best choice for mixing and blending powdery materials, liquid and powder.
Double helical ribbon mixer for powder mixing and liquid spray system is featured with shorter mixing time and better blending uniformity.