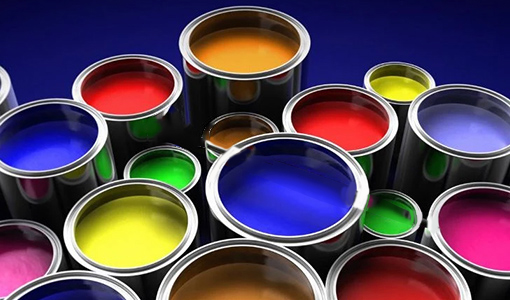
Gel coats (or gelcoats) are modified resins applied to molds in the manufacture of fiber-reinforced plastics. They are often used to provide a durable, colored and glossy surface to the finished composite but also serve other functions such as protection against UV damage, water absorption and chemical exposure.
Most gel coat formulations are based on polyester, vinyl ester or epoxy resins and normally contain pigments, fillers, thixotropic agents, promoters, inhibitors and other additives. The catalyst is typically added by the molder just prior to application of the gel coat.
Applications of High Speed Dispersers and Multi-Shaft Mixers:
- Battery Pastes
- Carbon Dispersions
- Catalytic Slurries
- Caulking Compounds
- Clay Dispersions
- Cosmetics
- Detergents
- Filled Epoxies
- Food Sauces
- Greases and Lubricants
- Gel coats
- Hot-Melt Adhesives
- Medical Gels
- Metal Slurries
- Paper Coatings
- Pigment Dispersions
- Plastisols
- RTV Compounds
- Rubber Solutions
- Sealants Solder Pastes
- Specialty Inks
- Toothpaste
- Woodworking Glue
High Speed Dispersers are well-proven in the processing of various coating formulations including gel coats used in fiber-reinforced plastics and cast polymers. Turning at tip speeds up to around 5,000 fpm, the saw-tooth blade of the High Speed Disperser generates a vortex on the liquid surface into which dry powder ingredients are added. Large and loose agglomerates are disintegrated by the disperser accompanied by an increase in viscosity. Acceptable flow patterns and turnover rates are easily achieved in products as high as 50,000 cP in viscosity.
A sample procedure is to charge the base resin (for instance, polyester polymer dissolved in styrene), followed by de-aerating and wetting agents. These are gently blended together and the mixer speed is then gradually increased until a deep vortex is formed. At this stage, thixotropic agents and fillers such as fumed silica, precipitated silica, calcium carbonate, talc, clay and/or aluminum trihydrate are added into the batch as quickly as the liquid will absorb them. Bulk additions are generally avoided to prevent large, dry lumps from forming. Once the powders have been thoroughly wetted out, other ingredients can then be added: pigments or dyes, promoters, inhibitors, UV absorbers and other specialty additives. Mixer speed is increased to maintain the vortex as the viscosity increases. The disperser blade may be located off-center to minimize air entrapment.
After all ingredient additions, it is usually beneficial to stop the disperser and scrape the side walls of the vessel to remove dry materials that may have gathered along the surface of the fluid. Mixing is then resumed for the final dispersion step. When supplied with a hydraulic lift, the disperser may be raised and lowered to eliminate “stratification” or possible layering within the batch
Multi-Shaft Mixers
Multi-Shaft Mixers are also widely used in the manufacture of gel coats. Equipped with two or more independently-driven agitators working in tandem, Multi-Shaft Mixers deliver a robust combination of high speed agitation and laminar bulk flow over a wide viscosity range. These systems routinely handle multiple recipes with great flexibility as the agitators can be engaged in any combination and at any speed for any interval.
The most economical design is the Dual-Shaft Mixer which features a disperser blade and a two-wing anchor agitator. The sweeping action of the low-speed anchor enhances the exchange of materials within the vessel, essentially “feeding” the disperser blade with fresh product. This supplemental agitation not only accelerates mixing but also dissipates heat that may be created by the high-speed saw-tooth blade. Another advantage to the Dual-Shaft Mixer is its closed system design which can easily be made vacuum-capable. Mixing under full vacuum helps to improve dispersion quality while producing a smooth, air-free gel coat.