Agitated Reaction Vessel is a heart of Chemical Industries & this is very important equipment used for Gas – Liquid reactions such as Hydrogenation, Oxidation, Formulation, Chlorination, Carbonation, reaction/ mixing of different type of chemicals in different conditions, pressure/under vacuum, temperature /cooling or at atmospheric conditions. . Vessel are used up to 40 kg./cm2 pressure & -30 oC to + 350 oC temperature.
We are manufacturing wide range of GMP/NON GMP Agitated Reaction Vessel from 100 litres to 50000 litres capacity in Stainless steel grade 304, 304L, 316, 316L, Carbon Steel , Alloy Steel, Mild steel (IS : 2062), Rubber lined & led bonded with outside M.S. or S.S. jacket for cooling /heating purpose with outside insulation also.
Manufacturing Standard
We are manufacturing as per ASME, DIN, BIS, IS, API, & C-GMP Standard Codes for pressure vessels for high quality job performance.
Agitator
We are manufacturing various type of stirrer for mixing/blending purpose like Anchor agitator, Turbine agitator, peddle agitator, Pitch agitator, Propeller agitator in variable speed as per the process requirement . Speed is reduced through reduction gear boxes & variable speed drive. we are using our MD make heavy duty bearing block with two nos. heavy duty bearings.
Testing
Vessel is tested on running condition for performance, vibration & leak test on desired pressure after completion of fabrication work. Outer jacket of vessel also hydro tested on desired pressure.
Internal Inspection & Documentation System
Vessel will be internal inspected by our Q.C engineer with complete internal record of inspection & Quality Inspection documentation.
Finishing & Painting
All inner & outer Surfaces of vessel are Prepared as per GMP Standard wherever required. All M.S. Parts are painted with one coat of red oxide primer & two coat & two coats of enamel paint after surface preparation.
Application of Agitated Reaction Vessel
Pharmaceuticals & Bulk Drugs, Distilleries & Beverages, Dyes & Chemicals, Pesticide & Insecticide, Dairies & Food product, Petro Chemicals, Fertilizers, Intermediates, Refineries & Allied Industries etc.
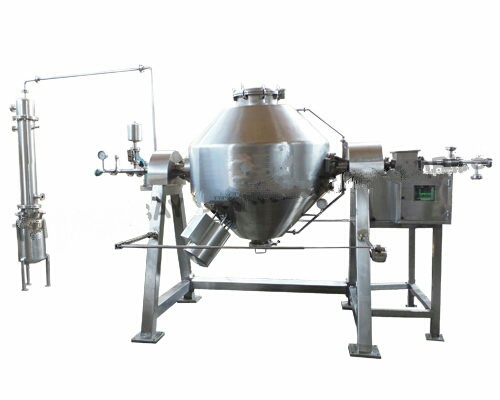
Roto Cone Vacuum Dryer is suitable for drying the material which can not operate at low Temperature easily oxidized, poisonous in nature. It operates at low Temperature efficiently under vacuum. It is very economical by total solvent recovery.
The roto cone vacuum dryer is equipment used in drying of products that are damaged by high temperatures and materials having special characteristics such as easily oxidized, strong irritants, poisonous dust and volatile compounds. The machine is also designed to release a product that is completely powdered and lump free.
Operational Mechanism
In operation, the rotocone vacuum dryer dries product through creation of a vacuum. This decreases the pressure around the product to below the vapor pressure of water and creates the effect of reducing product water boiling point which then evaporates and there is enhanced rate of drying of the product. The process is also done under low relative humidity for better drying.
Equipment Features
To enhance the rate of drying, the rotocone vacuum dryer manufacturers may add lump breakers onto the cone for breaking the large clumps of material inside the rotating cone, increasing the drying surface area and achieves more efficient drying.
Double Cone Vacuum Dryer
The double cone vacuum dryer also utilizes the vacuum drying technology with greater drying efficiency. Wet product goes through an indirect heating process and agitation with tumbling action, all while inside a vacuum to achieve rapid drying. In this process, recovery of solvent is also possible through condensation processes.
With constant innovation, the RVCD manufacturer has been able to deliver highly precise models that achieve thorough drying of product, uniformity of products, reduced drying time and an easy to clean and maintain machine. The roto cone vacuum dryer is mainly used in chemicals processing and pharmaceutical industries where air contamination can easily occur with other types of dryers.
Capacity
Standard models range from 50, 100, 325, 500, 750, 1000, 1500, 2000, 3000, 5000 Ltrs Rotocone Vacuum Dryer , Rotocone Vacuum Dryer Manufacturer, RCVD manufacturer, Double Cone Vacuum Dryer Manufacturer.
-
- Our machines are simple and effective method of drying wet cakes and sometimes slurries.
-
- Specially Uniform material shuffling over the heated contact surface of the rotocone dryers
-
- Drying time Reduces and eliminates need of re -drying of lumps.
-
- N2 pulse jet dust filter provided for better operational efficiency of products.
-
- discharge valve with Quick open able for direct packing of dry products into bags or drums.
-
- Best Suitable to process crystalline or amorphous powders which prone for lumps.
-
- cGMP construction with safety railing to avoid personnel injury.
-
- Available from 100 Ltrs. to 5000 Ltrs. gross capacity.
-
- Due to vacuum and agitation, it is possible to dry heat sensitive materials.
-
- No degradation due to over exposure, more temperature and time.
rotocone vacuum dryer working principle,
Rotocone Vacuum Dryer (RCVD) also called Rota Cone Vacuum Dryer is suitable for drying of materials which cannot resist high temperature, Material which are easily oxidized, volatile materials which should be retrieved, materials strong irritant and poisonous in nature. Abster Equipment Roto-cone dryer with improved technology integrates during operation under vacuum. The roto cone dryer facilities, enhanced drying efficiency, low-temperature operation, and economy for the process of total solvent recovery. It helps cGMP-based working by achieving optimum dust control while offering advantages of efficient charging and discharging of materials. The drying unit equipped with lump breakers initially breaks large lumps and subsequently powders them (in a single cone). The rotary action of the dryer together with the mechanical action of the breaker cuts down drying time and gives a lump-free product.
Vacuum dryers offer many benefits including:
- Unsurprising and Repeatable result.
- Dehydrated Temperature responsive Products -since all fluid vaporize at a lower temperature at condensed pressures, it is probable to vaporizes the fluid at very low temperatures.
- Concentrated Energy – because the vanishing of the fluid under vacuum occurs at a much diminish temperature; the temperature discrepancy is augmented with no raise the temperature.
- Protected for Friable goods – The low speed at which falls down dryer function, immediately a few revolutions per minute, makes Rotocone Vacuum Dryers (RCVD) perfect for subtle and friable solids such as agglomerated solids, macromolecules, or crystals.
- More absolute release – different agitated dryers, Rotocone Vacuum Dryers (RCVD) have an extremely modest exterior area and no protester to trap product. The easy unhindered 45-degree cone allows all goods to liberally release.
- Low Cross blemish – since there is only one stirring part, the tumble dryer is an intrinsically easy and clean intend, which improves surrender and abridged cross blemish.
- Without difficulty clean – The straightforward interior plan is perfect for maintenance with a solitary spray bar.
- Effortlessly inspect internal – All surfaces of the Rotocone Vacuum Dryer (RCVD) can be inspected from one vantage direct – the loading emerges.
- Avoid corrosion – The Rotocone Vacuum Dryer (RCVD) is perfect for avoiding corrosion of substance and with the adding of a motionless gas washout, oxygen free surroundings can be maintained.
SALIENT FEATURES/MOC (GMP Model)
Inner shell/cone and contact parts in SS316
Heating (H.W./Stream) Jacket in SS304
Insulation with the jacket in SS304
Cyclone separator in SS304
Drive unit enclosed with SS Covers
FLP motor and electricals
Provision for nitrogen purging
Digital temperature indicator (FLP) at hot water inlet and outlet
Digital temperature indicator (FLP)
Temperature and vacuum gauges (Dial type on cone)
Safety guard with limit switch. Pulse-jet type dust filter is provided inside the cone
Butterfly valve at the discharge
Positioning wheel for cone
Drive: Gearbox and motor direct coupled and box to cone drive shaft chain drive/Hbull gear and pinion
Construction and finish as per cGMP standards
OPTIONALS:
Digital temperature controller (FLP) with a pneumatic valve at the hot water inlet.
Lump breakers on the cone with FLP motor and dry mechanical seals
What is High Shear Homogenizer Mixer?
The high shear homogenizer is the machine that to shear, disperse and impinge the material through the high-speed rotation of the homogeneous head connected with the engine. In this way, the material will become more delicate and promote the fusion of oil and water. Widely used in cosmetics, shower gel, sunscreen, and many other cream products are used in the emulsifier. Food industry in the sauce, juice, etc. Ointment in the pharmaceutical industry. Petrochemical, paint, paint, ink and so on will be used high shear homogenizer
What is shearing homogenization?
Precision matching of rotor and stator, working head (rotor and stator forgings) claw structure, two-way suction, high shear efficiency.
Intermittent high shear dispersion emulsifying homogenizer is to form high frequency, strong circumferential tangential velocity, angular velocity and other comprehensive kinetic energy efficiency through high speed and stable rotation of rotor. Under the action of the stator, strong and reciprocating hydraulic shear, friction, centrifugal extrusion, liquid flow collision and other comprehensive effects are formed in the reasonable narrow clearance between the stator and rotor. The material is recycled in the above working process in the container, and the final product is obtained.
What Are the Application Areas of the High Shear Homogenizer Mixer?
Emulsifier has a wide range of applications, such as adhesives, paint coatings, cosmetics, food, medicine, plastic resin, printing and dyeing, ink, asphalt and other industries have a wide range of applications.
Fine chemicals: plastics, fillers, adhesives, resins, silicone oil, sealants, slurry, surfactants, carbon black, defoaming agents, brighteners, leather additives, coagulants and so on.
Petrochemical industry: heavy oil emulsification, diesel oil emulsification, lubricating oil, etc.
Daily chemical industry: washing powder, concentrated washing powder, liquid detergent, all kinds of cosmetics, skin care products, etc.
Paint ink: latex paint, inner and outer wall paint, water-based oil paint, nano paint, coating additives, printing ink, printing ink, textile dyes, pigments, etc.
Biomedicine: sugar coating, injection, antibiotic, protein dispersant, medicine cream, health care products, etc.
Pesticide and fertilizer: pesticide, herbicide, emulsion, pesticide additives, fertilizer, etc.
Food industry: chocolate shell, fruit pulp, mustard, residue cake, salad dressing, soft drinks, mango juice, tomato pulp, sugar solution, food essence, additives, etc.
Nano material: nano calcium carbonate, nano coating, all kinds of nano material additives, etc.
Road asphalt: ordinary asphalt, modified asphalt, emulsified asphalt, modified emulsified asphalt, etc.
Why Do You Need a High Shear Homogenizer Mixer?
Emulsions are the most widely used dosage form in cosmetics, ranging from watery fluids to thick creams. Therefore, the discussion of emulsions is of great significance to the research and production, as well as the preservation and use of cosmetics. In this way, the material will become more delicate and promote the fusion of oil and water.
What Are the Limitations of Using a High Shear Homogenizer?
High Shear Homogenizer most is batch processing, when batch materials over 1000L per batch ,It is difficult to ensure that the material in the vessel is evenly dispersed and sheared. So suggest match a homogenizer pump working together .
Beside capacity limitations , high shear homogenizer popular use slurry grinding , its rotor and stator high speed rotation to shear slurry particle size, it normal can reduce to micron grade , can not arrive nano size , if ask particle arrive nano size , need match with ELE bead mill
Which Components make up High Shear Homogenizer Mixer?
High Shear Homogenizer Mixer mainly composed of motor and Homogenizer head and base frame and electronic control system
Optional :Pneumatic lifting/ hydraulic lifting.
What are Quality Standards for Good High Shear Homogenizer Mixer?
Experienced customers know that,homogenizer head is most parts of high shear homogenizer, good quality high shear homogenizer must need good homogenizer rotor and stator as belo
1) Narrow rotor and stator gap
as you know the high shear homogenizer working principle is motor drive rotor in high speed rotate, high speed rotor and fixed stator forming a strong shear force to shear materials to micron size,like scissor, so of course is the rotor & stator gap more small , the shear force more high for materials
it more need precision processing, we adopt most advanced technology for rotor and stator ,rotor and stator can arrive mini 0.10-0.15mm clearance , when the motor rotate at high speed,it shear force very strong , thus homogenizer very good
2) precision forging rotor and stator
rotor and stator after forging will more hard, more durable use ,some factory for save cost , not forging for rotor and stator
Thus rotor and stator is soft , after use sometime , it will be worn , it will affect emulsion effect
What is the Principle of a High-shear Homogenizer?
Precision matching of rotor and stator, claw structure of working head (manufacturing of rotor and stator forgings), two-way suction and high shear efficiency.
The intermittent high shear dispersion emulsification homogenizer forms the comprehensive kinetic energy efficiency of high frequency and strong circumferential tangent speed and angular speed through the high-speed and stable rotation of the rotor; Under the action of the stator, strong and reciprocating hydraulic shear, friction, centrifugal extrusion, liquid flow collision and other comprehensive effects are formed in the reasonably narrow gap between the stator and rotor. The materials cycle through the above working process in the container, and finally obtain the product.
Intermittent high shear working process:
1. Under the centrifugal force generated by the high-speed rotating rotor, the materials in the figure are sucked into the working chamber from the upper and lower feeding areas of the working head at the same time.
2. The strong centrifugal force throws the material into the narrow and precise gap between the stator and rotor from the radial direction. At the same time, the material is initially dispersed and emulsified by centrifugal extrusion, impact and other forces.
3. Produce a linear speed of at least 15m / s at the outer end of the high-speed rotating rotor, up to 40m / s, and form strong mechanical and hydraulic shear, liquid layer friction, impact and tear, so that the materials can be fully dispersed, emulsified, homogenized, broken and ejected through the stator slot at the same time. The emulsifying machine shears, disperses and impacts the materials through the high-speed rotation of the homogenizing head connected with the engine. In this way, the material will become more delicate and promote the integration of oil and water. Sauce, fruit juice, etc. in the food industry. Ointment in the pharmaceutical industry. Emulsifying machines are used in petrochemical industry, paint, coating ink, etc. The application of mixing, stirring, dispersion, homogenization, emulsification and grinding in the process of experiment or industrial production.
4. The material is continuously ejected from the radial direction at high speed, changing the flow direction under the resistance of the material itself and the container wall. At the same time, under the action of the upper and lower axial suction force generated in the rotor area, the upper and lower strong overturning turbulence is formed. After several cycles, the materials finally complete the process of dispersion, emulsification and homogenization.
What Are the Factors Affecting the Efficiency of High Shear Homogenizers Mixer?
1. The form of the emulsifying head (batch type and continuous type)
2. The shear rate of the emulsifying head (the larger the effect, the better)
3. Tooth structure of the emulsifying head
4. The time that the material stays in the dispersed wall. (It can be regarded as the same motor, the smaller the flow, the better the effect)
5. Number of cycles (the more, the better the effect)
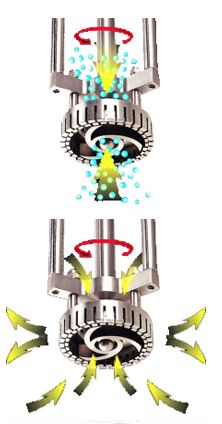
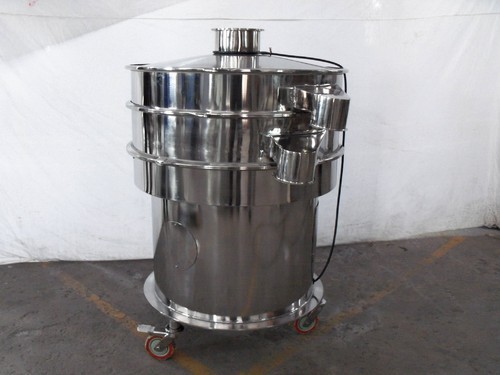
Vibro sifter is one of the needed types of machinery in many laboratory and industrial processes. It is used for the gradation of raw materials by separating materials based on their particle size. Ideally, these are circular unitary gyratory screens which are also referred to as vibrating sifters, control sieves, vibro sieves or check screen. Vibro Sifter is available in many configurations, design, capability, etc. depending upon their requirement or application in specific activities.
A Vibro sifter is not something unusual for the pharmaceutical or food processing industry and they are present in different categories depending upon size, the number of sieves, and specific application of equipment.
Working Principle of Vibro Sifter
Vibro Sifter works on the gyro principle. The word gyro here refers to Gyroscopic motion which is a tendency of a rotating object in order to maintain the orientation of its rotation. In machines, gyratory motion is obtained from specially designed gyro motor, which is fitted underneath the vibrating assembly. A specially designed rugged spring completely isolates this assembly from the base with the help of Gyro-motor. The motor is fitted with eccentric weights present at its as well as base to create centrifugal force. This whole assembly is covered by an SS plate.
Assembling a Gyro Machine
The deck hopper is also shielded from SS 316 sheet. A discharge port is provided on the hopper to collect the tangential discharge.
A charging port is connected to the Conical shape top lid. There is a screen fitted in between the hopper & top lid. The machine’s inner & outer surfaces are mirror polished.
How does Vibro Sifter Machine Work?
Firstly the material which we wish to separate is fed into the machine. Hopper acts as feeding for the machine. Then it is assured that the rest components such as cover, screen structure, and the base frame are tightly clamped. Once the machine is given the power the vibrating motor will create a motion and screen or sieve will start moving in the motion. Material for separation now starts moving towards sieve depending on the size of the particle. They move in a continuous flow and are exited through the other end of the machine.
Vibro Sifter Applications in Pharma Companies
Vibro Sifter is one of the crucial components for the Pharmaceutical company as it is used in the end process. Vibro sifter ensures that there is no contamination and offers assured particles in the end product.
We all know that preciseness is a must while we are manufacturing medicines as a slight increase or decrease in the quantity of the raw ingredient will alter the efficacy of the medicines. So, not only in end processes, but it can also be used while separating two or more ingredients from a mixture in order to weigh and create pellets. Thus, there is a need for such equipment in pharma companies. Besides Pharmaceuticals, the food and beverage industry also uses this machine.
The Conclusion
Abster Equipment is serving its pharma clients for a decade now. It is one of the respected names, well established brand in supplying the best packaging and process equipment for the Pharmaceutical industry. Based in Ahmedabad, it has not only tapped the domestic product, but has also explored the international markets and has been succeeding in both these markets.
Sigma Mixers (Kneader) is modern heavy-duty mixer specially designed to produce uniform mixing and kneading of highly viscous materials. this consists two shafts of ‘Z’ shapes blades moving in opposite direction at different speeds. Also available in stainless steel construction also and the system is also provided with jacket arrangement for handling heating or cooling application. The mixing action also involves combination of shearing, stretching, folding, dividing and recombining of material processed between sigma blades and container walls that ensure optimum results.
Sigma Mixer is available in capabilities of 5, 10, 25,50, 100, 250, 350, 500 with power support of 1, 3, 5, 10, 15, 20,25, 30 HP.
Specially designed for: The sigma mixer have application to produce highly viscous materials like different kinds of Chemical, Dyes & Pigments, Paint, Polymers Plastic, Putties, Plastic, Pharmaceuticals, Printing ink, stiff pastes, adhesives, polyester Compounds, flush colours, brake lining compounds, resign, soap, PVC coatings, Rubber compounds, Confectionery, Magnetic Tape Coatings, Ceramic, Carbon Black, doughs, Food Products, Fibre Glass, Grease, Lead Storage Battery, Soap & Detergent etc.
Operation of Sigma Blade Mixer
Material is loaded through the top of the container to typically 40 to 65 percent of the mixer’s total volumetric capacity. The rotation of the blades is through heavy duty drive systems typically consisting of a motor, gearbox, couplings, and gears. The tip speed of the sigma mixer is generally limited to 60 metres per minute. Mixing may be carried out at ambient temperature or under controlled temperature conditions. The mixer troughs can be provided with jackets for circulation of hot or cold media to maintain the required temperature conditions within the mixer. The discharge of the material from the mixer container is either by tilting of the mixer container. bottom discharge valve, or through an extruder / screw located in the lower portion between the two trough compartments. The mixer may be equipped with any one of these discharge arrangements.
Salient Features
Options Available with us:
Applications of Sigma Kneader
Capacity:
3 Ltrs. to 2000 Ltrs.
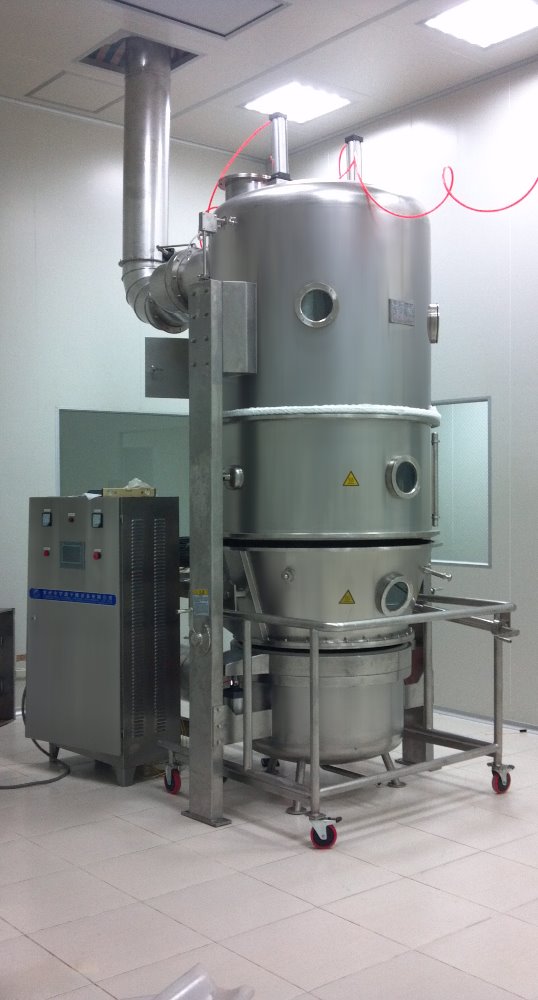
Fluid Bed Dryer or Fluidised bed dryer is a kind of equipment used extensively in the pharmaceutical industries to reduce the moisture content in raw ingredients like powder and granules. The working principle of this equipment includes fluidization of the fed materials. In this process, hot air at a high temperature and pressure is introduced in the system through a perforated bed of moist solid particulate. The solids are lifted from the bottom that are slightly wet in condition and are suspended in a stream of air (fluidized state). Heat transfer occurs as soon as there is a direct contact between the wet solid and hot gases. The dry gas takes away the vaporized liquid. The gas exiting is partially recycled, sometimes.
Working Principle of Fluid Bed Dryer
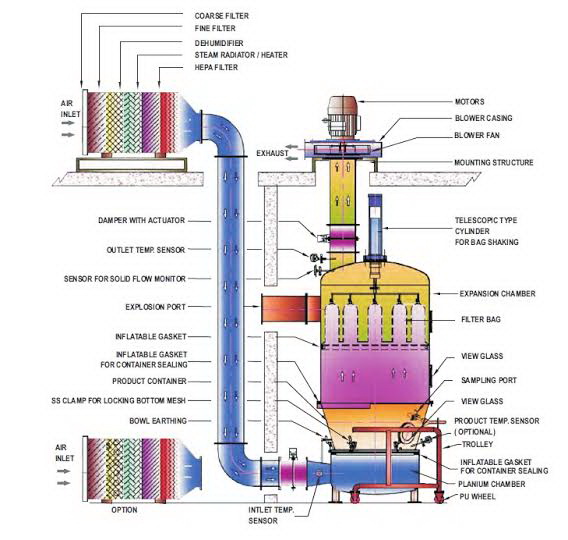
Fluid Bed Dryer or say Fluidized Bed Dryer is composed of a stainless steel chamber having a detachable bottom, which is often perforated and this is called the bowl. Through this perforated bottom, the air is introduced and with the help of heaters that increases the temperature of the air present inside. The heated air is then filtered and is allowed to pass through the bed of the material. Within the system, there is a provision for an attachment of a fan. The fan initiates and monitors the air flow direction. One can also regulate the air flow and the temperature at which the machine is working.
The Fluid Bed Dryer bag expands with the flow of air and powder particles start a turbulent motion. The material gets dry inside due to perpetual exposure to dry air. The material thus exiting the system is once again filtered.
Materials, after they are dried in a constant-rate drying, are processed via wet-bulb temperature. This process ensures that the ingredients dried through this process to low moisture content, under relatively low temperatures. One can achieve high drying results by installing the heat exchanging tubes or panels, which cover 80% of the heat exchange process. Due to the presence of a large heat exchange area inside the Fluidised Bed Dryer, the required gas amount is small. To check this issue, the sizes of each equipment of the system used in the system is minimized.
Where is Fluidised Bed Dryer Used?
A fluidized bed dryer is widely used in the granulation area of Pharmaceutical manufacturing. Granulation is a technique to dry the material in order to get the desired moisture content so that the manufactured medicines pellets are perfectly compressed.
Fluid Bed Dryer has a high drying rate, therefore, the material gets dried very quickly. Because of this property, this machine proves very useful in giving out high output.
Fluid Bed Dryer has been put in use to create synthetic resins. This machine can also be used in food, fertilizers, ceramics, Agrochemicals, etc. There is a machine type called B-FBD and this one is suitable for the material which requires drying in the decreasing-rate drying zone.
The Concluding Line
Abster equipment, having a decade-old history and headquartered in Ahmedabad has been supplying automated, semi automated machines that help Pharma Companies to get their desired output. The company offers a complete range of packaging equipment from the pharma companies present in domestic as well as international markets.